DTU Construct
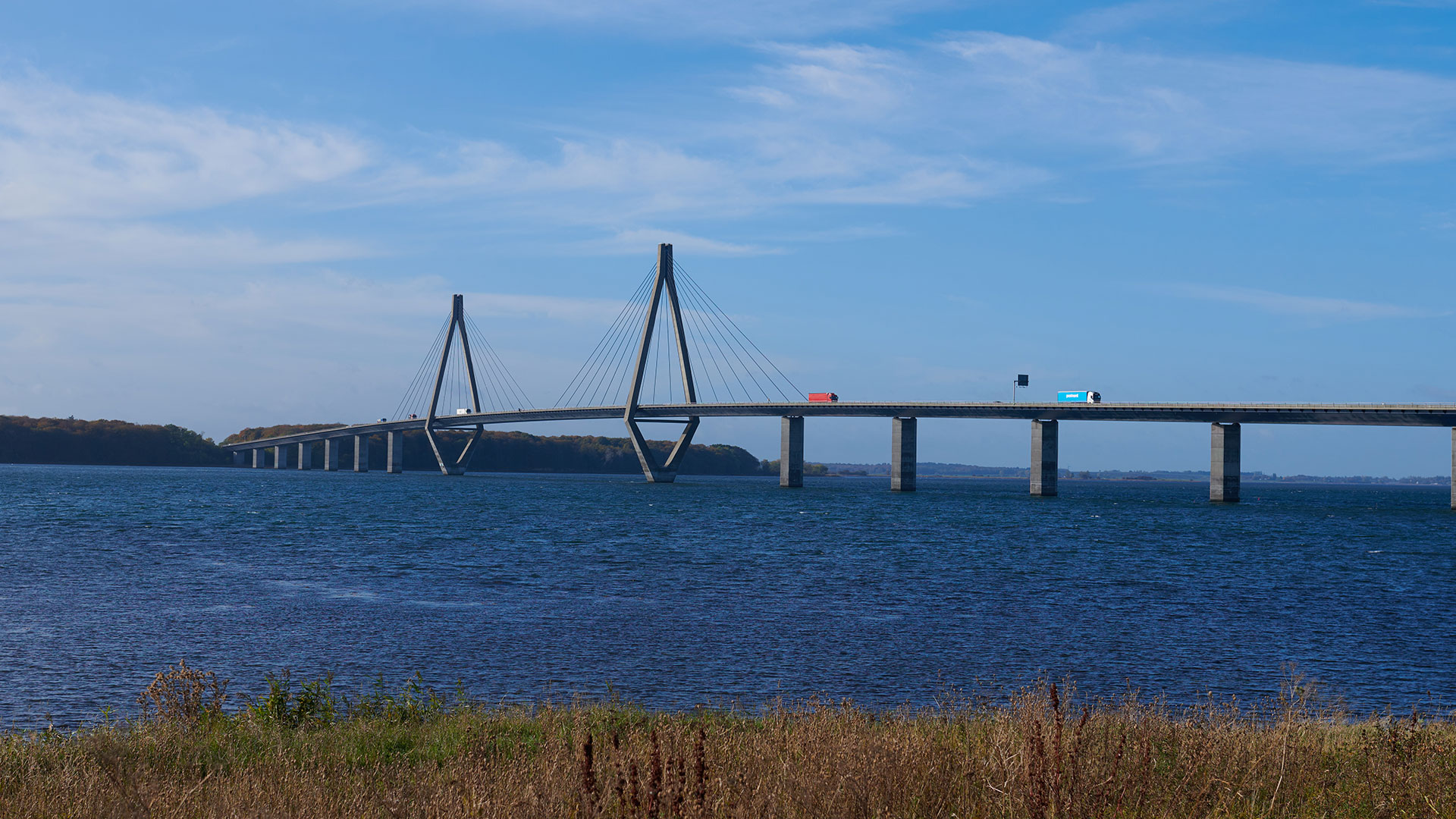
DTU Civil and Mechanical Engineering develops and utilises science and technical knowledge for the benefit of society and the sustainable development. We undertake research, education, innovation, and scientific advice of the highest quality within building design and processes, building construction and safety, building energy and services, solid mechanics, fluid mechanics, materials technology, manufacturing engineering, engineering design and thermal energy systems.
About the department
Easy access to information about the department